Introduction: Off Frame Modular Construction
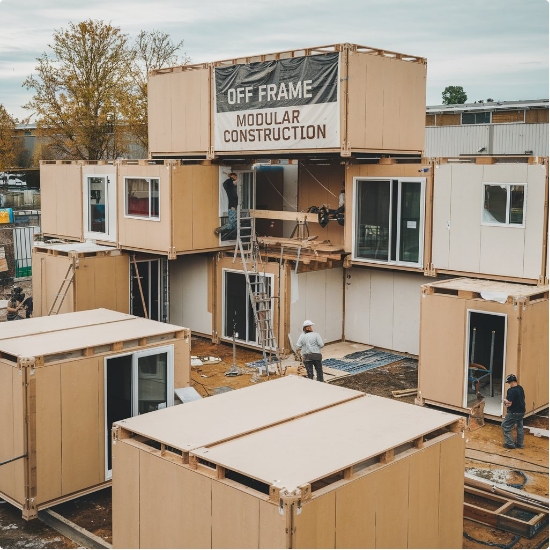
Off-frame modular construction is an advanced method of construction where complete modules are manufactured off-site and brought to the construction site for assembly. The modules in this method can also be relocated as they are not fixed to a foundation which expands the options considerably. This technique increases the rate of construction, minimizes waste, and provides a better control over quality. For programs where the time needed is short and design elements are varied, this method is appropriate. Modular buildings can be built with this method for residential, commercial, and industrial purposes. Off-frame modular construction is becoming increasingly popular.
Breaking Down Off-Frame Modular Construction
Off frame modular construction is a process, where building units’ construction is performed away from the building site and after transportation to the site these modules are assembled. Off frame modular construction is more advanced than traditional construction methods which construct a building at one site. Since the modules are completed such as interiors, finishes, fixtures, and fittings off the site, on site assembly is quick and simple.
This method has greatly contributed to reduction of construction activity duration and enhancement of quality control. The infamous weather and other such factors which adversely affect construction activities are minimized to the extent possible through the factory setting. This also implies enhanced predictability in project delays and a reasonable time frame for the completion of projects.
The Advantages of Off-Frame Modular Construction
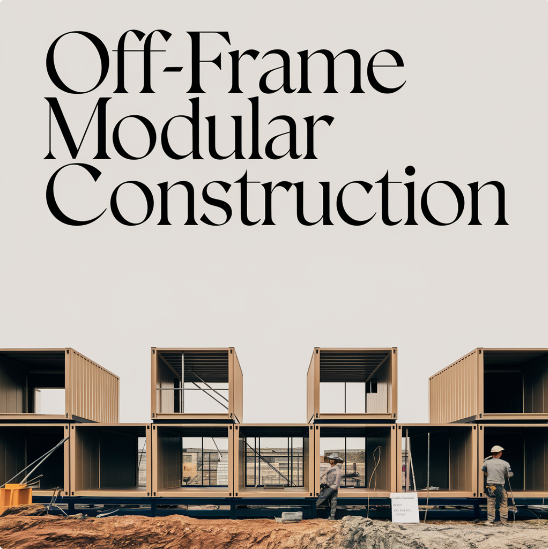
The off-frame modular construction method can be of great importance due to minimizing the time of the construction. The construction of the units and preparation of the site takes place at the same time so the completion of the constructed projects can be 50% – times quicker than the normal builds. That is useful especially in the cases when the project has very strict time frames or objectives to reach on the market very fast.
Off-frame modular construction also has advantages in monetary terms. The greater efficiency of production in factories results in reduced labor and wastage, and the systematic nature of such construction reduces the risk of hidden costs further. Thus, this approach is especially appealing to the developers who wish to cut down the costs and not quality of the project.
Quality Control and Sustainability
Quality management in a factory is still easier in comparison to that of a construction site. As a result of thorough inspection during the course of fabrication, standardization is enhanced and the possibility of defects is minimized. The result is more effective builds with fewer defects after the construction is completed.
Moreover, off frame modular construction offers distinctive advantages in terms of sustainability. The controlled space leads to reduced resource wastage which optimizes the overall construction process by using environment-friendly methods. Also, the construction, moving on-site, and assembling of modular buildings require less energy input which makes them more efficient than the conventional processes.
Challenges and Considerations
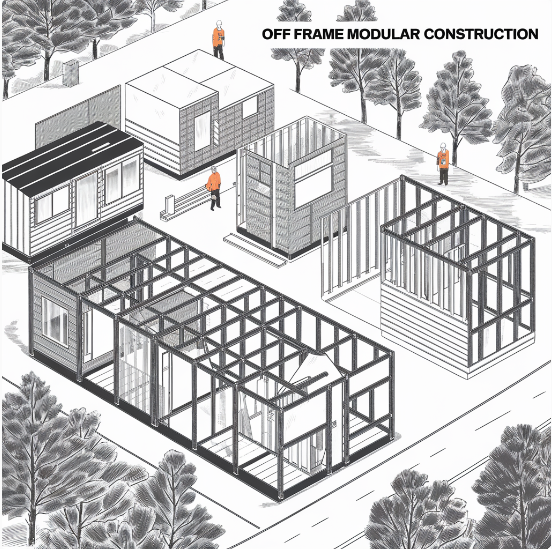
To begin with, the general benefits of off-frame modular construction do not come without their obstacles. One of the possible issues, for instance, can be the price, which tends to be higher during the initial costs, mainly because of the concentration incurred in providing the necessary facilities, manufacturing and logistical transport technologies. These costs, however, are frequently gained back through time and labor efficiencies that are realized in the future.
The other aspect to consider here is the absence of design choices. Modular construction would serve its purpose but may not be able to cater to multiple options including all the variety of features for modular construction; therefore it may also not be the best option for designs that are uniquely intricate for which structural engineering is concerned. In this regard, it is very important to seek the services of professional designers and manufacturers who have in-depth knowledge of modular construction.
Real-World Applications and Success Stories

Off-frame modular construction technology is being adopted in several sectors including, residential housing and commercial development. A case in point is “The Stack”, a high rise apartment building in New York City, which employed modular construction to cut down on the time and cost of construction while upholding quality output.
With teenage enrollment increasing in many communities, specialists in education are no longer ignoring modular solutions. To relieve the growth of pupils in the United Kingdom, the Department for Education has started through implementing modular construction of new comprehensive school buildings.
Future Trends and Innovations
The prospects for off-frame modular construction in the future seem bright given that new technological advancements are spearheading new possibilities. In modular designs, 3D printing and innovative building materials are being used increasingly, which increases efficiency and environmental sustainability.
As a result, the advent of digital technologies like Building Information Modeling (BIM) allows for the design and construction processes to be optimized since it enhances the planning and execution of the construction. Such trends are anticipated to elevate the modular construction process to a higher level, hence becoming more attractive to the developers and builders.
Making the Switch to Modular
If any of the challenging aspects deter you from off-frame construction, consider outsourcing it to qualified business practices that carefully weigh the benefits against the challenges. Leverage highly skilled professionals who are familiar with the particulars of the task and can bring you such custom solutions. In this way, you can benefit from modular construction in the delivery of superior quality buildings in a cost effective and sustainable manner.
FAQs: Off Frame Modular Construction

What is Off-Frame Modular Construction?
Off-frame modular construction is when a building or a house is put together piece by piece, where some pieces were built off-site in a factory. Borrowing from “off-frame” construction, the modules do not sit on top of a steel frame but, rather, on a conventional foundation, and therefore have the same visual and structural qualities of a house built at the site.
How does Off-Frame Modular Construction differ from a traditional site built house?
Both types of homes may have similar finishes, but off-frame modular homes have only the prospect of consistent quality finishes as they were built in a factory where quality is controlled and construction is usually quicker. The houses are off-site and pre-assembled on the construction site. In comparison, conventional homes are rather almost built entirely on-site, and thereby can lead to construction delays because of exposure of materials to weather elements.
Are Off-Frame Modular Homes durable and long lasting?
Off-frame modular homes can be said to be off-frame only if they apply to the building codes set out for the houses that are built at the site. Because construction happens mainly in a factory climate, materials are safeguarded from adverse weather conditions which would result in twisting or detrimental impacts. Furthermore, these homes are built for transportation, so their strength is quite impressive.
Can Off-Frame Modular Homes get modified according to the suit of the individual users?
Yes, perfection of any off-frame modular construction lends itself to a variety of options. External walls, and their layouts, but finishes, materials and home decorations can be tailored by the owners according to their needs. Most modular home builders can also build their modules in accordance with the client’s requirements to make the house fit his particular style.
What is the time required for building and delivering an Off-Frame Modular Home?
As for off-frame modular construction, it is usually faster than other types of building operations. It is common for most of the homes to be built inside a factory in a period of 6 to 8 weeks then brought to the field where it will take an additional period of 2 to 4 weeks for setting up because of site conditions and preparations needed. This varies for a home depending on its designs and the site where it will be constructed.
Conclusion: Off Frame Modular Construction
Off-frame modular construction innovatively changes the way construction is done and is associated with many benefits in terms of time, cost, and environmental impact. It relocates a large quantity of the construction activity to a factory where management is done in a controlled environment. This mitigates the amount of wastage, enhances the development of standards and general timelines. It also offers more design possibilities. Customized structures that are able to service different functions can be constructed.
With continuous improvement in technology and an increase in the rate of construction for quick turnaround time and less environmental impact, off-frame modular construction will certainly dominate within the construction modes during the near future. This new technique, when used, can help people to improve and enhance the way construction is done which in turn will change the way people make homes, office buildings, and other structures.